Велика енциклопедия на нефт и газ
Електролитен гланц
По време на полупериода на катода, пасивацията периодично се разрушава. Както при DC електролитно полиране, електролитите съдържат както вещества, които допринасят за образуването на пасивния слой, така и вещества, които улесняват разтварянето. [31]
Основният му принцип остава непроменен и до днес. След обезмасляване и киселинно ецване или след електролитно полиране алуминият се потапя в азотна киселина (1,42 g/ml) за отстраняване на замърсителите. [32]
Работата по проверка на машинните части е значително улеснена от електролитно гланциране или полиране, тъй като те надеждно разкриват всички дефекти на повърхността. Например, този метод се използва при периодично повторно тестване на лопатките на турбините. При термично обработени пружини от стоманена или пиано тел се откриват металургични дефекти и се премахва обезвъгления повърхностен слой, който е причина за разрушаване на умората. Този метод се използва също така за проверка на бутални щифтове, зъбни колела на помпата, клапани за случайни дефекти при термична обработка и шлифоване на пукнатини. По същия начин се изпробват изковки от леки метали за самолети. [33]
Това вероятно обяснява защо разредените химически вани за полиране обикновено не постигат гладкостта, която се получава при потапяне на електролити с концентрирани киселинни смеси. Освен това, висок огледален блясък не се постига при електролитни гланцови вани с техните плътно свързани пасивиращи филми. На фиг. 118, интерференционните линии ясно показват по-ниска микрогладкост на проба от 99 99% чист алуминий, полиран в баня с химически гланц, в сравнение с анодния гланц. [34]
През последните години има постижения в тази посока. Доставчиците на алуминий, неръждаема стомана и месинг вече могат да произвеждат специални класове от тези метали специално за електролитно полиране или полиране. [35]
От икономическа гледна точка използването на електролитно лъскане или полиране няма ефект в случаите, когато металните изделия се полират механично в автоматични машини. Това е особено вярно, когато се използва барабанно полиране. За разлика от тях електролитното гланциране или полиране ще бъде от полза, когато поради сложната конфигурация на частите е трудно механично да се полират или последната е по-скъпа. [36]
Времето за обработка е по-малко от минута; висока плътност на тока (около 100 A/dm2); напрежението е по-високо от това на другите електролити и може да достигне 40 - 60 V. Електролитното почистване е от полза при производството на скъпи части. Освен това едновременно се осигуряват предимствата на електролитния гланц на повърхността. [37]
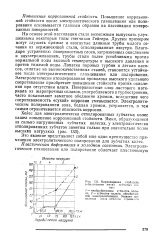
Друг пример са прави и извити дълги тръби от неръждаема стомана, полирани отвътре. Чрез елиминиране на повърхностни слоеве, замърсени с окисляване и карбуризация, тръбите стават по-устойчиви срещу нормална вода с висока температура и високо налягане и срещу тежка вода. Лопатките на парната турбина и частите на помпата, отляти от висококачествени стомани, стават по-стабилни след електролитно гланциране или полиране. Електролиран полиран проводник с високо съпротивление подобрява устойчивостта на окисляване при липса на влага. Повърхностните слоеве на топлоустойчивия сплавен листов материал, използван в турбостроенето, често показват забележимо изчерпване на хром, в резултат на което устойчивостта на суха корозия намалява. Бедната на хром зона се елиминира чрез електролитно полиране, като по този начин се ограничава рискът от корозия. [39]
Откриването на такъв ефект и прехвърлянето му в почти всички метали и сплави в началото почти не е било свързано с никакви икономически съображения. Безспорното развитие на електролитното гланциране (полиране) е постигнато предимно емпирично. Когато изглеждаше необходимо да се разшири методът с нови материали, решението обикновено се намираше във факта, че вече известните условия на работа бяха до известна степен променени. Интересно е да се отбележи, че прилагани от самото начало на развитието на метода в относително малък избор от химикали, все още съставляват по-голямата част от най-добрите съвременни електролити. Непрекъснатият напредък в електролитното полиране доведе както в лабораторната практика, така и в промишленото производство до подобряване на оборудването и условията на работа, независимо от теоретичните съображения. [40]
Механичното полиране, което кара повърхностния слой да тече, за разлика от електролитното полиране, променя повърхността, образувайки специален повърхностен слой. Въз основа на последните изследвания, този слой е микрокристалит и има различни химични и физикохимични свойства от метала под този слой. Тези промени се дължат на материалите, използвани за полиране, и на високите температури, които се развиват по време на обработката. На повърхността се появяват механични напрежения, които влияят върху свойствата на метала. Чрез премахване на изкривения повърхностен слой, електролитното гланциране или полирането оказва голямо влияние върху довършителните работи на металните материали. [41]
- Устройство за измерване на показалеца - Голяма енциклопедия на нефт и газ, статия, страница 1
- Токарно закалена стомана - Великата енциклопедия на нефт и газ, статия, страница 1
- Триизмерно разпределение - Велика енциклопедия на нефт и газ, статия, страница 2
- Подреждане - Великата енциклопедия на нефт и газ, статия, страница 3
- Филтрирано произведение - Велика енциклопедия на нефт и газ, статия, страница 1