Производство на сандвич панели
Като изолационен материал в сандвич панели използваме само висококачествена, практически не абсорбираща екструдирана полистиролова пяна (EPS) на американската марка Styrofoam Dow. Неговите предимства:
- Дълготрайна топлоизолация
(постоянство на характеристиките за дълъг период от време) - Висока механична якост (компресия, скъсване, огъване, срязване).
Позволява да се овлажняват високи динамични натоварвания, причинени от вятър и вибрации. - Високи характеристики на бариера срещу влага и пара
(важни фактори, влияещи върху трайността) - Химична устойчивост
- Добра адхезия
- Леко (ниско тегло)
- Стабилност на размерите (консистенция на геометрията на плочата)
Основни моменти, свързани с технологиите за сандвич панели
Залепени сандвич панели. При тях слоевете са свързани посредством едно- или двукомпонентно (по-често срещано) полиуретаново лепило във вакуум или механична преса (последното е доста скъпо, така че не всеки може да си го позволи). В същото време сандвич панелът може да бъде или трислоен: облицовка + изолация (с цел намаляване на разходите, някои използват пяна пластмаса, някои използват вътрешен EPS, а ние използваме американски EPS) + облицовка или петслоен с добавянето на шперплат под облицовката. На теория сандвич панелът може да се състои от повече слоеве.
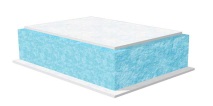
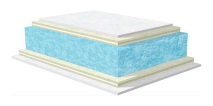
Използването на тази технология е най-подходящо за несерийни поръчки, тъй като себестойността на панела не се влияе от тяхното количество.
Напълнени сандвич панели. Облицовката на бъдещия панел се поставя в преса, като между тях се избира необходимото разстояние, а краищата се затварят с ограничители. Това разстояние ще определи дебелината на изолационния слой. Горната облицовка в пресата се държи или от магнити, или чрез вакуумни вендузи. По метода на пълнене се различават отворено и затворено пълнене. При отворения метод полиуретанът се излива върху една от облицовките при атмосферно налягане под въздействието на гравитацията. При затворения метод полиуретановата пяна се инжектира под налягане през тръба в пространството между облицовките. Най-трудното тук е да се постигне равномерно разпределение на пяната, т.е. равномерната му плътност в целия панел. За да се реши този проблем, изливането се извършва в няколко точки от единия край (най-дългия), а самият панел се накланя (така че пяната да тече по-бързо към противоположния край). Не винаги може да се използва отворено запълване: по този начин се правят само панели, които нямат вградени елементи. Методът със затворено пълнене е по-гъвкав, но трудоемък. Във всеки случай, намаляването на себестойността на излятия панел в сравнение с панела, направен чрез технология на залепване, се постига, когато се произвеждат поне дузина еднотипни фургони. Трудности възникват и при производството на N-слоеви панели: облицовките с вътрешни слоеве първо трябва да бъдат залепени във вакуум или механична преса, а след това полиуретановата маса се излива между тях (две преси работят вместо една → консумация на енергия, време за производство на панела се увеличава → интензивността на труда се увеличава, поради което 4- и 5-слоевите микробуси с PU пяна са доста скъпи.
Недостатъци на стиропора
EPS характеристики
Преди това имахме опит в използването на EPS, произведени в страната (умишлено не посочваме марката). На пръв поглед той се различаваше от внесения само по цвят (внос - син, вътрешен - жълт), но при подробно проучване се оказа, че:
- вътрешният EPSP има нестабилно качество: от доставката до доставката, плътността на материала варира от 35 до 40 kg/m³ (ние определихме това чрез претегляне на всеки брикет, теглото им варираше). В резултат на това микробусите загубиха голяма част от своята топлоизолация;
- размерите на плочите на домашния EPSP, дори в един брикет, се различават (грешката на геометричните параметри понякога достига 2 mm). Около 25% от материалите, които са влезли в производството, са били отписани като скрап. Затова направихме прехода към много по-скъпа изолация от американски стиропор с незначителни финансови загуби.
- RUSAL разширява производството си в Бокситогорска глиноземна рафинерия, общество и екология
- Производство на хот-дог, продажба на хот-дог, бизнес план за хот-дог
- Производство на съдове за еднократна употреба и цена на оборудването
- Производствен процес
- Собствен бизнес за производство на прибори за хранене