Вътрешни технологии "Romelt"
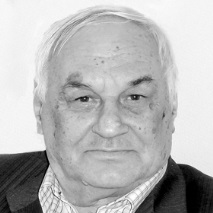
Доктор на техническите науки, директор на Иновационен център за научни изследвания и обучение "Romelt".
Историята на създаването на технология за производство на чугун от несъсредоточени суровини от желязна руда датира от Съветския съюз. В Московския институт за стомана и сплави (MISiS), където работя през цялото това време, професор Ванюков създаде технология за топене на медно-никелови руди в специален блок, който все още се нарича пещта Ванюков. В момента две такива пещи работят в Норилск, две в Балхаш и две в Урал. Когато висши партийни лидери посетиха нашия институт, те зададоха въпрос на учените: "Защо няма подобен, също толкова прогресивен процес в черната металургия?" И през 1978 г. в MISiS, под ръководството на професор Владимир Роменец, започва работа по разработването на такъв процес. Идеята е да се създаде алтернатива на производството на доменни пещи и да се стопи чугун без недостатъците, присъщи на доменната пещ. И сериозни недостатъци бяха и все още остават - необходимостта от коксови въглища (кокс), скъпи оскъдни суровини, както и необходимостта от внимателна подготовка на съдържащи желязо материали.
За да осъществи тази идея, ЦК на КПСС реши да построи пилотен завод в Новолипецкия металургичен комбинат (НЛМК). С помощта на московския Гипромез (генерален дизайнер), използвайки държавни пари, съгласно техническото задание на MISiS беше разработен проект за изграждане на пилотна промишлена пещ, способна да произвежда до 40 хиляди тона чугун годишно. Дизайнът на вече доказаната пещ на Ванюков е взет като прототип за агрегат за нов метод за производство на черни метали. На този етап, през 1984 г., се присъединих към проекта. По това време всички имаха практически нулеви познания в тази област - с изключение на идеята нямаше нищо.
За изпълнението на проекта MISiS създаде сектор за преработка на суровини от желязна руда (PZhS), който по-късно беше реорганизиран първо в лабораторията PZhS, а след това в Центъра Romelt. На базата на сектора PZhS бяха организирани изчерпателен изследователски екип и гостуващ екип, които включваха служители от отделите на института. С този екип работим от много години: изградихме пещта за година и половина, а от 1985 до 1998 г. усвоихме различни аспекти на технологията. Експериментите завършиха с успех, технологията беше разработена, призната от практиците и научната общност.
- След това започнаха да го въвеждат в производството?
Както казах, първоначално беше планирано доменните пещи да бъдат заменени с нови агрегати - това се оказа утопично предложение. В процеса на усвояване на технологията намерихме собствена ниша за този процес. Разбрахме, че няма нужда да се конкурираме с доменната пещ - това е агрегат, който ще служи успешно дълго време.
Трябва да се има предвид, че в металургията по време на експлоатацията на доменни пещи, конвертори и валцуващи цехове се образува маса отпадъци, така наречената утайка. Те съдържат не само голямо количество желязо и цветни метали (предимно цинк), но и елементи, вредни за процеса на доменната пещ, като натрий и калий, които влошават работата на доменните пещи и увеличават разхода на кокс. Следователно такива шлами от заряда (смес от изходни материали за производство на метал) са изключени. Разработената от нас технология, всички тези неща, поради особеностите на топенето, се смила. Рециклиране на отпадъци с добив на ценни метали и производство на чугун - това е една от нашите ниши. Втората ниша са главните звена на мини-фабриките. Това е преработката на бедни руди в чугун, който може да се използва в минизаводи като заряд, тоест вместо скрап. Доменната пещ, която произвежда три милиона тона чугун, може да храни голям град за 200-300 хиляди души. Но в същия Урал има много малки градове с 60-100 хиляди души - за тях нашите фурни могат да бъдат много търсени. Сега работим в тази посока: ангажирани сме с популяризирането и комерсиализацията на технологията, като същевременно продължаваме да я изучаваме - в нея все още има много бели петна.
- Защо не можете да отидете на големи обеми наведнъж?
Трябва да преминете през пътя на еволюцията. Подходът е следният: нека първо овладеем малки мощности - 100, 200, 300 и 500 хиляди тона, а след това да решим дали е необходимо да се овладеят големи мощности. Освен това доменните пещи все още работят и печелят. Защо да инвестираме, когато няма задачи? В същото време в същия Липецк или на Северстал се генерират 500-600 хиляди тона отпадъци годишно, от които могат да се получат 300 хиляди тона чугун. Тези обеми са точно за нас.
Между другото, доменната пещ е преминала по същия еволюционен път в своето развитие. Сега те са пет хиляди кубически метра, а в началото на пътуването бяха много по-скромни - 50-100 кубчета, не повече.
Металургичен завод в Мианмар, изграден по иновативната руска технология Romelt, разработена от учени от NUST MISIS. Главен изпълнител - Тяжпромекспорт.
- След като беше разработено техническото и дизайнерското решение, някъде се оказа, че е внедрено?
Още при съветската власт правителството на Съветския съюз издава указ за изграждането на два комплекса на базата на технологията на Ромелт: първият - в Липецк; втората - в металургичния завод в Кузнецк, за преработка на утайки от тези заводи с извличане на цинк от тях и тяхното обезвреждане.
Беше през 1990г. Година по-късно ситуацията в страната се промени и в завода дойдоха нови собственици. В завода в Новолипецк технологията на Ромелт беше незабавно възприета, но те се нуждаеха от завод за три милиона тона наведнъж. От своя страна се опитахме да обясним: „Не можеш да строиш за три милиона наведнъж, трябва да вървиш постепенно. Нека да строим за 300 хиляди. Няма да се конкурираме с доменната пещ. Нашата задача в Липецк е да преработваме утайки. " В резултат на това собствениците решиха, че преди всичко ще разработят продукти с висока добавена стойност и всички пари бяха изхвърлени.
- Как започнаха да работят в променена ситуация?
Преди това парите за експерименти и топене ни бяха отпуснати от Министерството на черната металургия и Липецкия комбинат, но от 1991 г. насам цялото финансиране спря. След това създадохме малко предприятие "Metekotech" и на пилотен завод, едновременно усъвършенствайки технологията, започнахме да произвеждаме чугун, продавайки го за производството на вани, радиатори и други подобни продукти. Спечелените пари бяха достатъчни, за да се нахрани малко, да нахрани лабораторията в института, да финансира научни изследвания и да плати на Липецк разходите за кислород и газ. Тоест сме преминали изцяло към самофинансиране.
По това време усвоихме работата с утайки и руда, в нашата инсталация често идваха чуждестранни индустриалци: американци, японци, индийци, китайци. При съветската власт бяхме малко притиснати в това отношение: „не казвай това“, „не казвай това“. И след като сами започнаха да продават чугун, видяха, че трябва да работят с хора. Няколко чуждестранни компании са закупили лицензи от нас за правото да използват технологията Romelt в Америка, Индия и Япония. За съжаление, в никоя от тези страни по различни причини случаят не вървеше добре. Тогава направихме най-далечния напредък в Индия. За изграждането на цех за преработка на утайки по технологията Romelt индианците отделиха площадка и проведоха търг, който бе спечелен от руската външнотърговска организация Tyazhpromexport. Заедно с индийския клиент Tyazhpromexport започва подготовката на договора, но в определен момент решава, че иска малко пари. Индийците обаче отказаха да преразгледат резултатите от търга. В резултат на това, поради несъответствие в капиталовите разходи, проектът беше спрян.
Съгласно условията на първите лицензи можем да работим само с три държави: Индия, Япония, САЩ, но сега възможностите се разшириха. Виетнам, Иран, Куба, Казахстан, Египет, Молдова, Северна Корея, Мианмар проявиха интерес към процеса на Ромелт. Що се отнася до Северна Корея, останахме с впечатлението, че те вече са построили Ромелт хитро.
- Ако заводът бъде пуснат по нова индустриална технология, тогава трябва да обучите подходящия персонал ...
В Индия никога не се стига до обучение. Но индийците имат добра научна школа, възпитана на металурзи, тоест имаше на какво да разчитат. Там има много добри учени, има добри изследователски институти, особено в областта на цветната металургия. Оборудването е страхотно. Но технологията Romelt има свои специфики и тя наистина трябва да бъде обучена. Бяхме готови за това: разработихме подходящи програми за обучение и необходимите инструкции за работа.
- След относителния провал в Индия някъде се стигна до реални поръчки?
Още по времето, когато Индия започна да ни се изплъзва, ние започнахме да взаимодействаме с Мианмар. Когато военните дойдоха на власт в Бирма (старото име на Мианмар), на страната бяха наложени тежки санкции. Доставките на желязо от чужбина намаляват, но има нужда от него (нещо около 200-300 хиляди тона метал). Тогава правителството на Мианмар решава да развие своя собствена металургия. Там имаше рудни находища, но нямаше коксуващи се въглища. И с въпроса как да се развие металургията в сегашните условия те се обърнаха към италианците - компанията Danieli. И "Даниели" по едно време се обърна към нас, дойде в Липецк и изучи нашата технология. Именно те препоръчаха Ромелт като обещаваща технология за Мианмар. И то си отиде.
- Tyazhpromexport отново беше главен изпълнител?
Главен изпълнител - Tyazhpromexport, генерален дизайнер - Ленинград Gipromez. MISIS - общ технолог. Като технолози, ние направихме всички инструкции за стартиране, аварийни ситуации, разработихме техническо задание, следвахме всички дизайнерски решения, работейки в близък контакт с главния изпълнител и проектантски организации.
Заедно с Tyazhpromexport си сътрудничим за популяризиране на технологията Romelt и на пазарите на други страни, извършваме предварителни проекти и технически и търговски работи. Подкрепата на тази организация е изключително важна за нас.
- За разлика от Индия, Мианмар е селскостопанска страна и на практика там няма технически подкован персонал. Това означава, че няма на кого да разчитате?
В Мианмар има сериозен недостиг на технически персонал, така че Центърът Ромелт трябва самостоятелно да обучава необходимите за завода специалисти. Първите етапи на обучение се провеждат в Мианмар, някои специалисти учат в Москва.
За да работи централата обаче нормално, са необходими около 800 технически специалисти. В допълнение към цеха Romelt е необходимо да се създаде и пусне в експлоатация инфраструктурата - това е кислородна станция, отоплителна централа, обогатителна работилница, цех за въглища, газоразпределителна подстанция и т.н. Общо 36 обекта, които трябва да функционират синхронно. Разбира се, това изисква технически персонал, който все още не е на разположение.
В момента Tyazhpromexport преговаря за организацията на обучение за 400 души, и то по следния начин. В Мианмар има колеж, в който можете да обучавате средно ниво: заварчици, механици, механици, сервизи, електротехници, обслужващи инструментална екипировка. А най-висшият ешелон, 80-90 души, трябва или да бъде доведен в MISIS за шест месеца, или да организира база на MISIS в Мианмар и да ги обучи там. По едно време, когато работехме в Египет, вече го направихме.
Парите отново се превърнаха в препъни камък. Мианмарците разбират, че персоналът трябва да бъде обучен, но не искат да плащат за това. Ние от своя страна не искаме да преподаваме безплатно.
Tyazhpromexport и MISiS също предложиха друга възможност: да изпратят около 150-200 руски специалисти в Мианмар, които по време на пускането на централата могат да стоят в ключови точки. От руснаците обаче много малко хора също разбират тази технология, но те могат да бъдат преподавани поне на родния си руски език.
Но във всеки случай в Мианмар очаквам трудности с пускането на редица оборудване и проблеми с местния технически персонал.
- Изминаха около 30 години от момента, в който започнахте да работите по технологията. Нещо се е променило в металургичната област през това време?
Ако разгледаме нещо, свързано с нашия проблем, тогава проблемът с утайките и преработката на бедни руди по целия свят само нараства. Същите индианци са натрупали цели полета утайки, има много находища на бедни железни руди. Същите проблеми са и в Казахстан. Технологично всяка утайка, съдържаща желязо, може да бъде преработена, но икономически не винаги е оправдана. Това решава екологичния проблем, но понякога не е изгодно. Но трябва да разберем, че трябва да платите за преработката на редица отпадъци, точно както ние плащаме за преработката на отпадъци. В същото време обработката на много утайки от заводи за черна металургия по процеса на Ромелт е икономически и екологично обоснована.
Разбира се, някои нови технологии за преработка на утайки и нискокачествени руди се появяват и се предлагат на клиентите. Почти всички от тях са тествани в лабораторни условия "епруветка". Когато ги обмислям за промишлено внедряване, винаги казвам: „Момчета, покажете ми колко тона метал са произведени по вашата технология“. В края на краищата 50-100 грама се топят в лабораторна пещ - чисто за наука. И за практика, за да влезете в индустриален завод, трябва да имате същата печка като в Липецк, за да вървите по нашия път. Но няма инсталации, които да произвеждат поне 100 кг метал на час. Това означава, че е невъзможно да се говори за реално индустриално внедряване на предлаганите в момента технологии, алтернативни на Ромелт.
- Вече виждате някои други точки на растеж за вашата технология освен Мианмар?
Нашият проект в Белорецк изглежда много обещаващ в това отношение, който се планира да бъде реализиран в град с 250-годишна металургична история с усилията на екипа на Белстал. Първо, все пак това е Русия. На второ място, проектът се подкрепя от правителството на Башкирия, предвижда се да се отделят федерални пари за него, градът е включен в списъка на едноиндустриалните градове. И трето, колективът в Белстал мисли много креативно и ние намерихме общ език с тях. За разлика от Мианмар, тук има реални противници и има дискусия, която ще помогне да се изгради по-добре и по-бързо. Ентусиастът на този проект, Рамил Бигнов, е известен предприемач в Башкирия, инвестирайки собствени средства в неговото изпълнение. Ако този проект бъде стартиран и продължи, мисля, че ще се превърне в отправна точка за по-нататъшно възпроизвеждане на Romelt както у нас, така и в чужбина.
Абонирайте се за eRazvitie.org във Facebook и VKontakte, за да не пропускате нови материали.
Можете да се абонирате за нови материали тук: Facebook VKontakte
- Лазерни технологии при лечение на остри хемороиди - Клиники на Беларус
- Лечение на болестта на Пейрони при мъже в Новосибирск, Медицински център - Alpha Technologies
- ЗНАЕТЕ - ИНСТИТУТ ПО ИНФОРМАЦИОННИ ТЕХНОЛОГИИ - g
- За VEDA - естествени здравни технологии
- Домашни леярни - леярни