Практическа работа No2
Тема: „Изборът на технически средства за диагностика на оборудването,
неговите системи и монтажни единици "
1) запознайте се с методите и средствата за диагностика на металорежещи машини;
2) придобиване на опит в комплектоването на диагностичната система на металорежеща машина, нейните възли и възли с инструменти и оборудване.
1) инструкции за работа;
2) машинно ръководство.
Оптимално използване на режещата машина:
Осигуряването на производителността и ефективността на металорежещите машини се постига:
- правилният избор на режими на рязане (скорост, подаване и дълбочина на рязане);
- достатъчна производителност (минимално възможното време за цикъл, осигуряване на необходимите скорости за работа на възлите и частите, осигуряване на необходимите силови ефекти);
- висока надеждност на машината (т.е. надеждност, издръжливост, износоустойчивост на възлите, работоспособност на възли и инструменти, поддръжка на машината, безопасност по време на транспортиране и съхранение на основните технически характеристики);
- качеството на машинния инструмент (точност и твърдост на оборудването, точност и грапавост на обработваните повърхности);
- високи икономически показатели (ниска консумация на енергия, висока ефективност, минимални експлоатационни разходи, минимален разход на работна течност, охлаждаща течност и др.);
- спазване на всички правила за безопасност за този тип машини (функциониране на необходимите блокировки, наличие на капаци, кожуси, предпазители). Индикаторите за шум и вибрации не трябва да надвишават допустимите стойности и т.н.
В допълнение, за надеждно и дългосрочно използване на металорежеща машина, поддържайки я в добро състояние, е необходимо да имате оптимална поддръжка и наличност на информация за техническото състояние на машината, което се осигурява от методите на техническа диагностика, чиито важни елементи са правилният избор на наблюдавани диагностични параметри (CDP) и технически средства. диагностика (STD).
Основните KDP на металорежещи машини, както и основните методи и средства за тяхното управление (технически диагностични инструменти - TSD) са дадени в таблица 2.1.
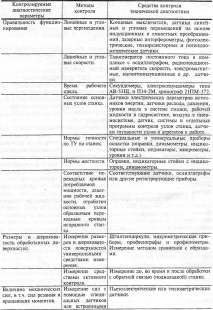
Таблица 2.1– Основни наблюдавани диагностични параметри за
металорежещи машини и методи за тяхното управление
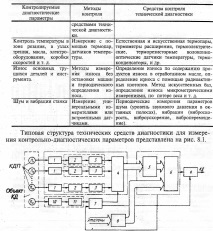
Продължение на таблица 2.1
Типична структура на технически диагностични инструменти за измерване на контролни и диагностични параметри е показана на фигура 2.1.
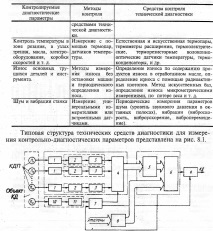
7 - блок за управление; 8 - стандартно устройство с памет; 9 - устройство за документиране на данни; 10– сензор за синхропараметър; 11 - синхронизиращ генератор.
Фигура 2.1 - Типична структура на диагностичните инструменти, измерващи CDP:
TSD определя с определена надеждност стойността на KDP, регистрира и предоставя анализ на обработката за вземане на решения относно съответствието или несъответствието на текущото техническо състояние на ДЧ.
TSD е средство за събиране, регистриране, обработка, отразяване и документиране на KDP.
Нивата на приложение на TSD, измерени с този KDP, някои характеристики на TSD са показани в таблица 2.2.
Таблица 2.2 - Нива на приложение на техническите диагностични инструменти
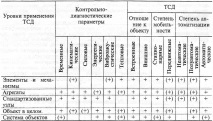
Някои видове TSD сензори са показани в таблица 2.3.
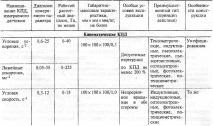
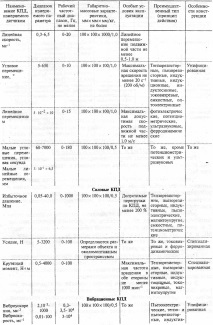
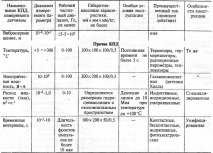
Разработването на диагностичен алгоритъм е един от важните етапи при създаването на системи за събиране на информация за техническото състояние на МС.
Най-простата диагностична задача е задачата, при която се определя само дали диагностичният обект е в работно състояние или не. При решаването на този въпрос се проверява изпълнението на всички изисквания на нормативната и техническа или проектна документация.
Много по-трудно е, когато е необходимо да се идентифицират не само неработещи обекти, но и дефекти на необходимата дълбочина на търсене.
Тоест да се определят дефектите на възлите и частите, водещи до неизправност на MS и AL. За това в броя на KDP трябва да се въведат допълнителни знаци, които позволяват търсене на дефект на дадена дълбочина (сред възли и части).
При избора на допълнителен KDP едновременно трябва да бъдат изпълнени три изисквания: броят на тези параметри трябва да бъде минимален и сложността на диагностиката да е минимална, а самият процес на диагностика е достъпен за автоматизация.
Напоследък широко разпространени са електрическите диагностични методи, по време на изпълнението на които се определят параметри, които не са предвидени от GOST или технически спецификации. В допълнение, електрическите диагностични методи получават сигнали, които са удобни за обработка, а също така ви позволяват да създавате прости, практически инерционни и безопасни диагностични инструменти, които могат лесно да бъдат автоматизирани.
При разработването на диагностичен алгоритъм е необходимо да се вземат предвид режимите на работа, работещи в MS и AL, температури, налягания, ускорения и вибрации, климатични и биологични влияния и др.
Отстраняването на неизправности при работата на MS и AL трябва да започне с прости и очевидни проверки: наличието на напрежение в мрежата и на входните контакти на машината, целостта на предпазителите, определянето на неработещи възли (машини, конвейери, асансьори, машини за управление) на вградени системи (хидравлични, механични, електрически, пневматични, електронни и др.) монтажни единици (възли), възли и накрая части.
Най-пълната информация е информация за причината за повредата на ниско ниво, което гарантира минималните разходи за нейното отстраняване. Колкото по-високо е нивото на източника на информация (нивото на диагностика) в структурното дърво на диагностиката (Фигура 2.2), толкова по-ниска е пълнотата на информацията и толкова повече разходи са необходими за търсене на причините за отказ.
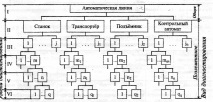
Когато търсите причините за неизправност (съставяне на алгоритъм за отстраняване на неизправности), трябва да вземете предвид препоръките за типични неизправности в ръководството за машината, експлоатационния опит на MS и AL, както и опита на експлоатация на подобни MS и AL, или подобни единици и системи.
Фигура 2.2 - Общ изглед на структурното "дърво" на диагнозата
автоматична линия с твърда връзка
Възможните дефекти и начините за тяхното отстраняване са показани в таблица 2.4.
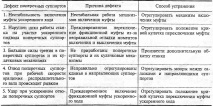
Таблица 2.4 - Таблица на дефектите и начините за тяхното отстраняване за отделни механизми на машината модел 1A225-6
Работна поръчка:
1. След като получихме задачата, съгласно таблица 2.5 изясняваме състава на възлите, възлите и системите, включени в машината по задачата.
2. Съгласно таблица 2.1 ние избираме KDP, както и методи и средства за техническа диагностика за машината като цяло, както и части, възли, възли, системи.
3. Изясняваме състава на диагностичната система на машината съгласно таблици 2.2
и 2.3 с посочване на всички KDP STD.
4. Анализирайте неизправността на машината, посочена в задачата. Избройте причините, причиняващи тази неизправност.
5. Контурни проверки, които ви позволяват да изясните причината за неизправността и да изберете реда на тяхното поведение, т.е. да напишете алгоритъм за отстраняване на неизправности.
6. Регистрирайте резултатите от работата.
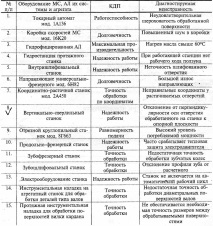
1. Списък на техническите диагностични инструменти, използвани върху металмашини за рязане и задачите, които решават.
2. Основните причини за загубата на точност на машината?
3. Как да открием износването?
4. Каква може да е причината за мощно увеличена консумациясти?
5. Поради това, което увеличава цикъла на машината?
6. Какви системи на металорежеща машина са подложени на повишено нагряване?
7. Кои са основните неизправности на металорежещите инструменти?
8. Какво характеризира увеличаването на шума и вибрациите на металорежещата машина?
- Практическа работа номер 1-2
- ПРАКТИЧЕСКА ЧАСТ, За пословици и поговорки, Притчи и поговорки, включително букви
- Грунд за основата, готов и подготвен, работа по приложението му, съвети от строители
- Практическо използване на пирамидите в човешкия живот
- Ремонт на тавана в апартамента, разходите за работа в Санкт Петербург