Метод за производство на глинозем
Притежатели на патента RU 2564360:
Изобретението се отнася до металургията, по-специално до киселинни методи за получаване на алуминиев триоксид, и може да се използва при обработката на алуминиеви съдържащи суровини, включително нискокачествени.
Недостатъците на този метод включват продължителност, ниска производителност и значителни топлинни разходи за нагряване на пара до необходимата температура, ако е необходимо, доставянето й по време на целия процес. В допълнение, 20% концентрация на солна киселина, подавана за киселинната обработка на суровините, не е оптимална и по-добри резултати при превръщането на алуминия в разтвор се постигат с използването на по-силна киселина.
Най-близък до заявения метод е методът за получаване на алуминиев оксид, разкрит в патентна заявка ЕР 0094081 А2 (IPC C01F 7/30, публикуван 1983 г.), включително обработка на алуминиеви съдържащи суровини със солна киселина, отделяне на кристали от алуминий хлорид хексахидрат от бистрия хлориден разтвор и двустепенното им термично
разлагане, за да се получи металургичен алуминий, докато парата непрекъснато се подава към втория етап на термично разлагане. Според този метод първият етап на термично разлагане се извършва при 200-400 ° C, а вторият етап при 900-1100 ° C.
Основата на изобретението е задачата за разработване на метод за солна киселина за получаване на металургичен глинозем, включително от нискокачествени суровини, което прави възможно преработването на бедни високосилициеви руди и отпадъци.
Техническият резултат е да се подобри качеството на алуминиевия оксид и да се намали консумацията на енергия с висока производителност на процеса.
Постигането на горния технически резултат се постига от факта, че в метода за получаване на алуминиев триоксид, включително обработката на съдържащи алуминий суровини със солна киселина, изолирането на кристали на алуминиев хлорид хексахидрат от избистрения хлориден разтвор и техния двустепенен разтвор термично разлагане за получаване на алуминиев оксид, вторият етап на термично разлагане се извършва при температура 150-450 ° C и непрекъснато подаване на пара със съотношението на общата маса на подадената пара към масата на получения алуминий -5,7.
Положителният ефект от въвеждането на водна пара започва да се проявява при стойност 0,2 в заявения диапазон. В 5.7 достига
максимум, а по-нататъшното увеличаване на консумацията на пара води до непродуктивни топлинни загуби.
Термичното разлагане на алуминиев хлорид хексахидрат е вариант на неговата хидролиза (термохидролиза), но в техническата литература обикновено се нарича калциниране и се представя чрез обобщеното уравнение:
Всъщност процесът преминава през междинна поредица от трансформации на основни алуминиеви хлоридни соли (оксихлориди) с различна основност и степен на хидратация. Някои от тези междинни и не винаги последователни реакции могат да бъдат записани като:
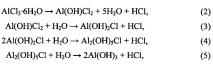
Реакцията (2) протича с отделянето на вода, което в излишък от стехиометрия е достатъчно за завършване на цялостната реакция (1). Въпреки това, според литературните данни и резултатите от нашите собствени изследвания при температури от 100-500 ° C, процесът спира, когато материалът е смес от алуминиеви оксихлориди, тъй като водата под формата на пари бързо се отстранява от реакционната зона, без да има време да реагира с междинни продукти на разпадане чрез реакции (3) - (пет). По-нататъшни трансформации са възможни само когато температурата се повиши до 900-1000 ° C в присъствието на димни газове, какъвто е случаят в прототипа. Освен това значителна роля тук играе водата, съдържаща се в продуктите от изгарянето на органично гориво. Тази пара обаче не е достатъчна, за да завърши бързо и ефективно образуването на алуминий.
Методът за получаване на алуминиев триоксид е както следва.
Съдържащата алуминий суровина се излугва със солна киселина, твърдата фаза се отстранява и кристалите на алуминиев хлорид хексахидрат се изолират чрез изпаряване на бистрия хлориден разтвор или осоляване с газообразен хлороводород. Отделените кристали се нагряват в произволно избран печен агрегат при температура 110-250 ° C до образуването на алуминиеви оксихлориди и забележимо инхибиране на по-нататъшни химични трансформации поради консумацията на вода, отделена по време на дехидратацията на първоначалния продукт (първи етап ). След това парата се подава в пещта при съотношението на общата маса на подадената пара към масата на произведения алуминиев триоксид, равна на 0,2-5,7, и процесът се прекратява (втори етап). Достатъчно е температурата на втория етап да се поддържа на нивото от 150-450 ° C, което значително намалява топлинните загуби и претендираното съотношение на общата маса на подаваната пара към масата на произведения алуминиев триоксид в рамките на 0,2-5,7 позволява минимизиране на разхода на топлина за прегряване на пара, в зависимост от избрания тип пещ, тъй като условията на взаимодействие на твърд материал с газова (парна) фаза са различни.
Чрез подаване на водна пара само до втория етап на разлагане на алуминиев хлорид хексахидрат се постига намалена консумация на пара при
високо качество на алуминиев оксид и производителност на процеса. Предварителна оценка показва, че по този начин е възможно да се намали общата консумация на топлинна енергия по време на разлагането на алуминиев хлорид хексахидрат с 1,5-2 пъти.
Методът за получаване на алуминиев триоксид е илюстриран със следните примери.
Същото се отнася за температурната стойност от 450 ° C (горната граница на декларирания диапазон). Тук, в зависимост от времето на престой на материала, изискването за съдържанието на алфа фазата може или не може да бъде изпълнено (пример 12).
За промишленото прилагане на метода е препоръчително да се използват два последователни блока на пещта, които позволяват двустепенно разлагане на алуминиев хлорид хексахидрат в непрекъснат режим с подаване на водни пари само към втория блок.
- Начини за получаване на голяма реколта от домати (домати) - моите методи за грижи, селекция, сортове и т.н., Сайт за
- ТОП 10 начина да забогатеете бързо и лесно
- Устройство и методи за почистване на комина за печката Бавария
- Прекрасни начини за забременяване - каква техника помогна на кого
- ЧЕРНА МАГИЯ И МЕТОДИ НА ПОСТАВЯНЕ, Аркрас