Бързи фризери
Фризерът GKA-2 (фиг. 1) е направен под формата на хоризонтална камера, разделена от преграда на две отделения. В долното отделение има охлаждащи батерии 1, в горното отделение 4 има вентилационен блок 2 и водачи на нива 3, по които продуктът се движи. Краищата на четните и нечетните редове на рафтовете са изместени на равни секции, благодарение на това каретките 8 (с четири ходови ролки) и тавите с продукта, поставен върху тях, могат да извършват вертикално зигзагообразно движение, преминавайки от горния рафт към основното.
Вътре в отделението 4 каретки с тави се движат по нечетните рафтове (1-ви, 3-ти, 5-ти отгоре) в една посока и по четните рафтове (2-ри, 4-ти, 6-ти отгоре) в обратна посока. Това движение се извършва с помощта на тласкащ механизъм, направен под формата на сдвоени вертикални гребени 5, чиито зъби са разположени над водещите рафтове. Зъбите на гребените са скосени, което осигурява плавно спускане на крайната каретка с лист за печене от горния рафт към долния.
За товарене и разтоварване на продукта служи маса за повдигане и спускане 6. При преместването му надолу Г-образните ограничители отварят капака 7 на прозореца за разтоварване и каретата с листа за печене излиза на маса 6. След това, листът за печене се придвижва към конвейера, а каретката, намираща се на масата, се издига, като поема по две тави с храна. В горното положение ограничителите отварят вратата на зареждащия прозорец, през който листът за печене с пресен продукт влиза в каретата и след това заедно с него се избутва върху горния рафт с гребен.
Работата на фризера GKA-2 при точка на кипене на амоняк от 40 ° C [t/ден (kg/s)]: зелен грах, череши, череши в кутии 10 (0,12), зелен грах в насипно състояние 15 (0,18), пипер в насипно състояние 10 (0,12), домати в насипно състояние, царевица в кочан 12 (0,14), сливи в насипно състояние 15 (0,18). Температурата на въздуха в апарата е -35 ° С; повърхност на охладителните батерии 925 м2; скорост на въздуха над продукта 7 m/s; производителност на вентилатора 7,7 m 3/s; мощност на двигателя на вентилатора 10 kW, двигател на конвейера 1 kW; продължителност на цикъла на замразяване 3600,15 840 s (1,4,4 часа).
Тунелните фризери работят непрекъснато. Бързото замразяване се постига чрез излагане на охладен въздух, движещ се по продукта с висока скорост, чиято температура е 30 ° С.
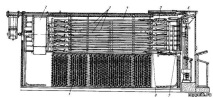
Фигура: 1. Бърз фризер GKA-2
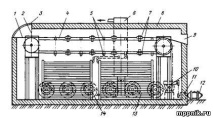
Фигура: 2. Тунелен фризер
Тунелният фризер (фиг. 2) има корпус 8, покрит с коркова изолация с дебелина 400 mm. Той има две батерии с директно разширение 13; охлаждащата им повърхност е 252 m 2. Над батериите има транспортьор 4 с мрежест ремък с ширина 2 м. Разстоянието между центровете на конвейерните барабани е 10 м. Работните и празните части на лентата се поддържат от опорни ролки 5 и по краищата - чрез водещи ролки 7.
Конвейерът се задвижва от електродвигател 12 през червячна предавка 11 и регулатор на скоростта 10; с помощта на този регулатор можете да настроите времето на замръзване от 2,5 до 3,5 ч. От същия регулатор на скоростта конвейерът получава периодично (периодично) движение; това позволява, в моментите на спиране, да зареди транспортьора през товарния отвор и да го разтовари през отвора 9.
Продуктовите кутии се поставят в камерата за предварително охлаждане 1; за това капак 3 се затваря с гумена завеса 2. В момента, в който конвейерът спре, изхвърлящата лента премества кутиите от камера 1 към конвейера. Течният амоняк се подава в сепаратора 6, откъдето по тръбопроводите постъпва в батериите на изпарителя. Изпарението става при температура от -33,3 ° C. След това парообразният амоняк излиза в горната част на сепаратора за течности 6 и от него влиза в компресора.
В сепаратора за течности нивото на амоняка се поддържа от поплавков регулатор. Циркулацията на въздуха се осъществява посредством шест аксиални вентилатора на работното колело 14, разположени от едната страна на батериите. Охладеният въздух се засмуква от вентилатори от дъното на батерията и се изпомпва през канали до горната част на корпуса; оттук охладеният въздух излиза на мястото, където е разположена работната част на колана, на която се намира продуктът. Плодовете в картонени кутии след замразяване имат температура -18 ° C. Производителността на апарата е 400 kg/h; габаритни размери на устройството 11 500 x 3650 x 2300 мм.
Недостатъци на тунелен фризер: големи размери; недостатъчно използване на обема му, което води до значителни загуби на студ; нарушена циркулация на въздуха, в резултат на което продуктът се замразява неравномерно по ширината на колана; топлинни загуби през захранващия отвор. Освен това недостатъкът на този апарат е, че може да се използва само за замразяване на продукти с един размер.
Апарати за замразяване на храни в азот (страничен продукт при производството на кислород) се използват все по-често в консервната промишленост. Течният азот се изпарява при температура от -195 ° C. Неговите пари са насочени със скорост от 35 ... 40 m/s към продукта и в резултат на голямата температурна разлика той замръзва за няколко минути.
Фризерът има тунел, разделен по дължина на три секции. Конвейер с мрежест ремък от неръждаема стомана преминава през целия тунел, транспортирайки продукта, който трябва да бъде замразен. Над конвейера, във всяка секция, има барокамера, в дъното на която са фиксирани дюзи, насочени към продукта. В първия участък на тунела продуктът се охлажда до температура на замръзване; във втория - той е замразен, а в третия - "втвърден". Във втората секция на изпарителя се получава изпаряване на азота; Азотните пари от изпарителя се издухват в камерата чрез вентилатор и се насочват през дюзите към продукта. Вентилаторите от първата и третата секция поемат азотни пари от втората секция и ги подават през барокамерите и дюзите към продукта. Количеството циркулиращи азотни пари се регулира в зависимост от температурата на сместа. Налягането на азотните пари в тунела е малко по-високо от атмосферното, което предотвратява проникването на външен въздух и влага и следователно вътре в апарата не се образува снежна обвивка.
Тестовете показват, че 90% от консумирания студ се изразходва за извличане на топлина от продукта и 10% - за компенсиране на топлинните потоци от вентилатора, конвейера и тунелните стени.
Възможността за използване на азот се определя чрез икономически изчисления; в същото време може приблизително да се приеме, че 1 kg течен азот, изпарявайки се и след това нагрявайки се до -25 ° C, е в състояние да даде около 376,8 kJ/kg (90 kcal/kg), което е достатъчно за охлаждане и замразяване 1 кг продукт до - 18 ° C.
Фризерите с много плочи се използват за замразяване на плодове, зеленчуци, рибни филета и месо в картонени кутии. В тези устройства топлообменът между хладилния агент и продукта се осъществява през преграда (стена).
Устройствата работят както с директно изпаряване на течен амоняк, така и със саламура.
Дизайнът на апарата в частта, в която се доставя и отстранява хладилният агент, зависи от неговия тип.
Многоплочният бърз фризер, работещ със саламура, е направен под формата на шкаф с една или две врати, през които продуктът се зарежда и разтоварва, опакован в картонени кутии. Вътрешните размери на шкафа са 1757 x 1230 x 1600 мм. В шкафа, хоризонтално една над друга, има 11 плочи с размери 1320 X 1000 x 40 mm. Плочите са изработени от алуминиева сплав и имат зигзагообразен канал вътре, през който се движи саламура, охладена до -25. -30 ° C. Горната плоча е неподвижна; всички други плочи могат да се движат вертикално нагоре или надолу по специални водачи. Плочите се задвижват от хидравлично бутало, задвижвано от налягане 1,0 на маслото. 1,2 МРа; маслото се изпомпва от зъбна помпа през маслен приемник.
Когато плочите се повдигнат, пролуката между тях се фиксира от дървени ленти, положени по краищата, чиято височина е с 2,3 мм по-малка от височината на кутията. Общото максимално повдигане на плочите е 625 мм. Когато долната плоча се движи нагоре, тя се опира върху горната с ламелите, повдига я, докато се срещне със следващата плоча и т. Н. Кутиите с продукта са здраво затегнати между две плочи, но не се смачкват поради дървените летви, фиксиращи празнина.
Саламурата влиза и излиза от плочите през тръби, свързани с маркучи към вертикални колектори; чрез една охладена саламура се подава към всички плочи; през другата, нагряваният разсол се отстранява за охлаждане. Скоростта на циркулация на саламурата в плочите е 0,2. 0,3 m/s.
Устройството работи периодично; изпълнението му зависи от броя на продуктите, заредени едновременно, продължителността на замразяването, товаренето и разтоварването.
Показателите за ефективност на апарата при замразяване на продукт до температура от - 18 ° C са дадени в табл. един .
един. Характеристики на устройството
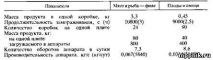
Фризерите с много плочи имат еднакъв дизайн, работещи с директно изпаряване на амоняк в каналите на плочите; структурно такива устройства се различават от описаното по-горе само по устройството на устройства за подаване на течност и отстраняване на парообразен амоняк.
Устройството има 11 плочи с размери 1300 x 1100 x 40 mm, изработени от алуминий с зигзагообразна намотка. Течният амоняк с температура -30 ° C навлиза във вертикалния колектор през поплавъчен клапан и след това през маркучи към всяка плоча. Колекторът е свързан с приемник за течен амоняк, разположен над апарата. Амонячните пари се засмукват от всяка плоча през маркучи до втория колектор, откъдето се насочват към компресора.
Основните недостатъци на фризерите са: относително ниска производителност, което налага инсталирането на голям брой устройства и води до увеличаване на разходите за обслужващ персонал;
използването на ръчен труд при замразяване на продукта в кутии и особено в матрици (подготовка на продукта, опаковане в кутии, товарене, разтоварване, преместване);
невъзможност на устройства за едновременно зареждане на продукти с различни размери и различни дебелини;
честотата на работа на апарата, свързана с необходимостта от товарене и разтоварване на продукта;
ниска производителност на устройствата поради висока термична устойчивост в точката на контакт между кутии (форми) и плочи.
- Гнездо за заваръчна машина 250А
- ЗАМРАЗЯВАЩО УСТРОЙСТВО превод от руски на английски, превод от руски на английски
- Слухови апарати и въпроси
- Пристрастяване към слуховите апарати към вашето дете, Phonak
- Свързване на енкодер към микроконтролер, програмиране на PIC микроконтролери