ПРОГНОЗИРАНЕ НА ОТКАЗИ НА АВТОМАТИЧНИ СИСТЕМИ ЗА УПРАВЛЕНИЕ НА БЛОКОВЕ ПОМПИ НА БАЗА НА
В момента Русия преминава от регистриране на свършен факт към използването на инженерни методи за предварителен анализ и изследване на високорискови обекти с цел предотвратяване на произшествия. Тече интензивна работа в областта на осигуряването на безопасността на работа на техническите системи, разработват се методи за определяне на надеждността на техническите системи, оценка на риска, подобрява се законодателната и регулаторна рамка.
Актуалността на проблема с надеждността се дължи както от увеличаване на сложността на производството с използване на нови технологии, така и от големи структурни промени в икономиката на страната, които доведоха до смущения в областта на финансирането, високи прогресивни нива на износване на дълготрайни активи, спад в технологичната и производствената дисциплина и намаляване на квалификацията на персонала, прехвърляне на срокове за ремонт и подмяна на оборудване, опростяване на рутинната поддръжка.
През последните години са проведени специални проучвания за оценка на риска и безопасността на производството. Извършва се мащабна оценка на безопасността на индустриалните предприятия с цел допълване на съществуващия подход и установяване на по-обосновани критерии [6].
Единната система за доставка на газ (UGSS) на Русия е уникална по отношение на производствения капацитет, организационната структура, естествените и климатичните условия на работа, технологичните специфики и други показатели. Мащабът на UGSS и неговата основна роля в енергетиката и икономиката определят изключителното значение на проблема с неговата надеждност.
GPU е ключов елемент на цялата система за пренос на газ, поради което ролята на контрол, диагностика, контрол и защита на GPU е възложена на системата за автоматично управление (ACS). Стабилността на цялата газопреносна система (GTS) до голяма степен зависи от надеждността и безопасността на газопреносната техника и техните системи за управление.
Предвид огромния брой графични процесори и графични процесори на ACS в GTS на страната, разработването на конкурентна програма за модернизация и подмяна на оборудването с ограничени ресурси, значимостта на задачата за оценка и прогнозиране на техническото състояние на GTS съоръженията не може да бъде сравнено.
В техническата диагностика прогнозирането на техническото състояние на даден обект се състои в оценка на възможното му състояние в определен момент от бъдещето въз основа на известна информация за настъпили промени в миналото и резултатите от определяне на действителното състояние в момента [7].
F (Z, t) = A (Z, t) + X (Z, t),
където A (Z, t); X (Z, t) - съответно детерминирани и случайни компоненти на процеса.
Ако степента на влияние на втория компонент в израза е незначителна, процесът на промяна на състоянието на обекта се описва като детерминиран, в противен случай той трябва да се счита за случаен. Изборът на един или друг подход се извършва според резултатите от анализа на външните условия и режимите на използване на обекта.
Това обяснява използването на два принципа в техническото прогнозиране - детерминистичен (аналитичен) и вероятностен. В първия случай резултатът от прогнозата са преките стойности на търсените параметри, във втория - техните вероятностни оценки [7].
За да се реши проблемът с прогнозирането, времето за използване на обекта се разделя на два интервала: T1 е интервалът за наблюдение на състоянието на обекта (в миналото и настоящето) и T2 е интервалът, през който се извършва прогнозирането (в бъдеще). Колкото по-голям е интервалът T1, толкова по-голямо е количеството информация за естеството на процеса на промяна на състоянието на обекта и толкова по-надеждна е прогнозата. Увеличаването на интервала на наблюдение обаче води до увеличаване на разходите, свързани с експериментални изследвания и обработка на резултатите от диагностиката. Надеждността на прогнозата зависи и от дадено време в областта T2 [7].
При решаване на проблема с детерминистичното прогнозиране в директна формулировка, необходимите характеристики са стойностите на диагностичните параметри. Тъй като получаването на аналитични зависимости и формирането на класове с голям брой диагностични параметри е свързано със значителни трудности, за прогнозиране техният минимум се задава от условието за осигуряване на необходимата надеждност на прогнозата. На практика обикновено се използва един диагностичен параметър - определящ или обобщен (като например индекса на техническото състояние). Ако не е възможно да се установи една определяща диагностична характеристика за обект като цяло, прогнозирането се извършва от неговите елементи, всички или най-отговорните. В този случай производителността на обекта в региона Т2 се оценява по най-лошия от получените резултати.
Проблемът с вероятностното прогнозиране се свежда до оценка на показателите за надеждност на даден обект в дадени моменти от времето в региона Т2. В този случай процедурата за прогнозиране и надеждността на получените резултати до голяма степен се определят от количеството първоначална информация за надеждността на обекта и неговите елементи. Най-универсален е методът за прогнозиране, основан на контрола на диагностичните параметри.
При случаен характер на промяната в състоянието на даден обект и, следователно, неговите диагностични параметри, вероятностната прогноза може да бъде изчислена само въз основа на резултатите от наблюденията на група идентични обекти, работещи в еднакви или подобни условия. Изчислението се основава на факта, че характеристиките на положението на случаен процес са неслучайни функции на времето.
Така прогнозирането се извършва на два етапа. На първия етап се изчислява прогноза за математическото очакване и дисперсията на определящата диагностична характеристика в даден момент от времето в областта Т2. На втория етап тези стойности се използват за изчисляване на вероятността от безотказна работа или вероятността от повреда на обекта.
Ако вероятностното прогнозиране не успее да установи един определящ диагностичен параметър за обект като цяло, прогнозирането се извършва от неговите елементи. В този случай показателите за надеждност на обекта в зоната Т2 се изчисляват в зависимост от вида на структурната логическа схема на обекта.
Предлага се подход за определяне на степента на риск от повреда на оборудването, което дава възможност за оценка и прогнозиране на техническото състояние на съоръжението с най-голяма надеждност. Този подход е своеобразно продължение на методологията за оценка на техническото състояние на обект с помощта на индекса на техническото състояние (ITS) [1].
Оценката на техническото състояние се основава на система от индикатори, чиято конфигурация е свързана със структурата на оборудването. Въз основа на тази информация се формира единна база данни за оценка, която отчита влиянието на различни параметри и различни структурни единици върху оборудването като цяло. Количествената оценка на техническото състояние на оборудването е безразмерна числена стойност, която се нарича ITS и се получава в резултат на определен алгоритъм [1]. Стойността на ITS характеризира състоянието на обекта от гледна точка на съответствие на неговите параметри със стандартните стойности, като се отчита значимостта (теглото) на всеки параметър.
Параметърът е паспортната характеристика на оборудването или характеристиката, получена в резултат на диагностика или проверка на оборудването. За да се получи безразмерна ИТС, количествените и качествените стойности на параметрите се преобразуват в целочислени дискретни стойности, които отразяват степента на съответствие на параметъра с неговата номинална стойност.
Оценката на техническото състояние на оборудването включва няколко етапа, представени под формата на диаграма (фиг. 1).
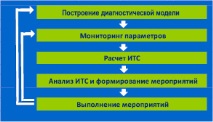
Фигура: 1. Етапи на оценка на техническото състояние
В [1] като скала за ИТС беше предложена 100-бална скала, където 100 е най-доброто съответствие с номинала, 0 е най-лошото. В съответствие с тази скала се определя техническото състояние и съответно неговата надеждност, както като елемент на системата, така и на системата като цяло.
Всички изчислени ИТС се въвеждат в обща база данни за анализ и разработване на подходящи мерки в зависимост от стойността на ИТС. След изпълнението на препоръчаните мерки параметрите се наблюдават и ИТС се преизчислява. По този начин, съгласно методологията, моделът за оценка на техническото състояние непрекъснато се коригира и подобрява, което прави възможно изчисляването на ИТС с максимална степен на надеждност.
По този начин ITS е цялостна оценка, която интегрира в своята цялост влиянието на всички необходими фактори. ITS проследява текущото състояние на елемента, т.е. детерминирания процес на промяна на състоянието на обекта. С помощта на ИТС обаче няма начин да се проследи внезапната повреда на даден елемент (случаен процес).
На фиг. 1 за периода 0 - s ITS се промени от a на b по определена крива. Подобна промяна в състоянието е доста лесна за диагностициране на практика, тъй като тя се променя постепенно и естествено. Това обаче е идеализирана ситуация, която е фундаментално различна от раздела, при който внезапно мигновено скачане на ИТС се случва от b на 0. Най-голям интерес представлява прогнозата за момента x (c; b).
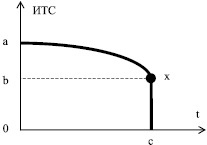
Фигура: 2. Графично обяснение
В момента много производствени предприятия дават MTBF като основни технически характеристики. Това е препоръка за прогнозиране на неуспехи. Тази стойност обаче има идеализирана основа, тъй като се използват общи статистически данни, които не отчитат специфичните експлоатационни условия на съоръжението. На практика тази точност просто не е достатъчна, за да се предскажат надеждно отказите на оборудването. Като примери за такива условия може да се посочи инсталация, климатични условия, вибрации, шум, индукция на електромагнитно поле и др. Дори мястото, което този елемент ще заема в цялостната система, ще определи средното време между отказите.
По този начин, ако за един случай (операция в производство 1) елемент ще бъде повлиян от набор от условия A, то за друг случай (операция в производство 2) същият елемент ще бъде повлиян от набор от условия B.
За да се реши такъв проблем (вероятностен прогнозен проблем), се предлага следният подход. Необходимо е в конкретно действащо предприятие да се поддържа частна статистика на отказите през целия жизнен цикъл на даден елемент, за да се изчисли степента на риск - вероятността за отказ. По този начин ще получим стойността на риска директно за конкретен случай, като по този начин ще я приближим възможно най-близо до истинската стойност. Трябва да се отбележи, че степента на риск е постоянна стойност, но за конкретни производствени условия тя е различна. Трябва да се отбележи, че предложеният подход е особено приемлив за сектора на транспортиране на газ поради голямата дължина и брой единици унифицирано оборудване.
Степента на риск се отнася до очакваната честота или вероятност от повреда на оборудването. По този начин използването на концепцията за степента на риска ви позволява да прехвърлите опасността в категорията на измеримите количества. Степента на риск всъщност е мярка за опасността. Трябва да се отбележи, че степента на риск също е безразмерна стойност в диапазона от 0 до 100, което носи допълнително предимство, когато се използва заедно с ITS.
В резултат на интегрираното използване на двете представени стойности (ITS и степента на риск) за оценка и прогнозиране на техническото състояние на съоръженията ще бъде предоставена пълна информационна подкрепа за вземане на решения за намаляване на броя на неизправностите на оборудването. На тази основа ще се извърши планиране, отчитане на изпълнението на работата и като цяло изборът на стратегия за повишаване на надеждността.
Рецензенти:
Иванов А.А., доктор на техническите науки, професор в Катедрата по автоматизация на машиностроенето, Нижегородски държавен технически университет Р.Е. Алексеева, Нижни Новгород;
Кретинин О.В., доктор на техническите науки, професор в Катедрата по автоматизация на машиностроенето, Нижегородски държавен технически университет Р.Е. Алексеева, Нижни Новгород.
- Нуждата като универсално свойство на живите системи и като основа за мотивационни процеси, Безплатно
- Прогноза за неуспех
- ПРЕДВИДЕНИЕ НА ОТКАЗ превод от руски на английски, превод руски на английски
- Прогнозиране - неуспех - Велика енциклопедия на нефт и газ, статия, страница 2
- Система за управление на съдържанието InfoDisk