Предварително смачкване на материал в челюстни трошачки
Грубите материали обикновено се подлагат на предварително смачкване. Целта на предварителното смачкване е да се получи материалът в такава форма, че да стане възможно допълнителното му смачкване. Най-големият размер на парчетата материал, влизащи в предварителното смачкване, зависи от размера на входа на дробилката, наречен устието, а степента на смачкване може да варира в определени граници от съответната промяна в размера на изхода на дробилката, наречена сплайн . Материалът се подава предимно механично.
В челюстни трошачки материалът се смачква чрез смачкване, като се притиска с движещата се буза на машината към неподвижната. Натрошеният материал пада от машината по време на обратния ход на подвижната челюст.
При челюстните трошачки периодично се извършва приближаването и отстраняването на подвижната челюст към неподвижната. В зависимост от метода на укрепване на подвижната челюст се разграничават дробилки:
- с най-голям замах в вратовръзката фиг. единадесет);
- с най-голям размах във фаринкса (фиг. 1, 2);
- с равномерно движение на бузата (фиг. 1, 3).
Дизайн на трошачка. Челюстната трошачка с най-голямо люлеене в вратовръзката е показана на фиг. 2.
Фигура: 1. Схеми на движение на валове в трошачки.
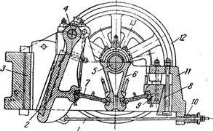
Фигура: 2. Челюстната трошачка с най-голямо люлеене в сплайна:
1-пръчка: подвижна буза; 3-фиксирана буза; 4-ос на подвижната буза; 5-ексцентричен вал; 6-свързващ прът; 7-дистанционни пластини; 8-регулиращи клапани; 10-пружина; 11-легло; 12-маховик; 13-ролка.
Всички части на трошачката са разположени в масивна чугунена рамка 11, която е подпряна на здрава тухлена или бетонна основа. При големите трошачки рамката е изработена от разглобяеми стоманени отливки или заварена от стоманени плочи с дебелина 25-50 мм. Раздробяването на материала става в работното пространство между подвижните 2 и фиксирани 3 бузи, оборудвани с подвижни оребрени плочи, изработени от специална стомана. Страничните стени на работното пространство също са защитени от подвижни плочи. Подвижната буза е окачена на неподвижна ос 4 и е настроена в колебателно движение от ексцентричния вал 5 посредством свързващ прът 6/шарнирно свързан чрез лостове (дистанционни пластини) 7 с тази буза и регулиращи клинове 8 и 9. Чрез преместване клиновете, чието относително положение може да се променя при използване на болтове, те регулират ширината на изходния слот и съответно степента на смилане на материала. Прът 1 и пружини 10 създават напрежение в движещата се система и осигуряват обратно движение на бузата.
Парчета материал се смачкват, когато свързващият прът 5 се издига, в резултат на което подвижната челюст 2 се доближава до неподвижната. Когато свързващият прът е спуснат, отворът на трошачката се отваря и натрошеният материал пада от работното пространство. Манивелата, образувана от свързващия прът и дистанционните плочи, е в основата на този тип трошачка и позволява много високо налягане.
Челюстните трошачки се характеризират с размери на гърлото и снаждането. Челюстите на тези трошачки се износват най-много и затова са направени подвижни и изработени от устойчив на износване материал. Изборът на метал за бузите зависи от естеството на материала, който ще се смачква: за по-меки материали, бузите са направени от избелващо желязо, за твърди материали - от отливка манган или хром стомана.
Бузите могат да бъдат гладки или оребрени; гладките бузи се използват за фино смачкване и за чупливи материали, а оребрените за грубо смачкване и за твърди материали.
Компресионните дистанционни плочи са направени от чугун с избелени краища или от стомана; напречното сечение на една от плочите се взема така, че да се счупи, ако материал с прекомерна твърдост, например парчета метал, случайно попадне в трошачката, тоест би служил като предпазител.
Предимствата на челюстните трошачки са надеждността на конструкцията, отварянето на изходната челюст, когато подвижната челюст се движи назад, лекотата на поддръжка, възможността за подмяна на части и сравнителната компактност на инсталацията.
Челюстните трошачки обаче имат и недостатъци: 1) силно разклащане на сгради поради дисбаланса на трошачката; следователно челюстните трошачки не са инсталирани на горните етажи на сградите; 2) прекъсвания в работата, дължащи се на повреда на някои части (разделителни плочи на свързващия прът, а понякога и рамката) поради влизане на парчета метал в работното пространство заедно с натрошения материал; 3) запушване на работното пространство с натрошен материал с неравномерно подаване на парчетата, което може да се избегне само при ръчно натоварване.
Челюстните трошачки се произвеждат в различни размери и видове, от малки лабораторни такива с размер на устието 150X100 mm, и завършващи с трошачки с размер на устата 2100x3000 mm. Последният може да смила бучки материал с обем 1-2 м3 и да има капацитет до 1000-1500 т/ч с мощност на задвижване до 300-400 кВт.
Челюстните трошачки се използват широко за грубо смачкване на материали с висока твърдост.
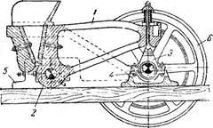
Фигура: 3. Челюстна трошачка с най-голямо люлеене в устата:
1-подвижна буза; 2-ос; 3-свързващ прът;
4-ексцентричен вал; 5 легла; 6-маховик.
Дробилката, показана на фиг. 3, има най-голямо люлеене в гърлото, когато има долна ос за люлеене на подвижната буза. Подвижната буза 1 е масивен лост, люлеещ се около оста 2. Дългото рамо на подвижната буза е свързано с ексцентричния вал посредством свързващ прът 3 4. Ширината на процепа се регулира чрез сдвоени болтове с помощта на от които лагерите на оста се преместват в специална водеща рамка.
Тъй като най-голямото размахване на челюстта при тази трошачка се случва в гърлото, а не в решетката, широчината на изходния слот остава постоянна по време на работа и смачканият материал е по-равномерен по размер на парчетата. От друга страна, натрошеният материал, натрупващ се в долната част на трошачката, може да я задръсти, което е съществен недостатък на този тип трошачки. Те се използват главно за смачкване на материали с ниска твърдост.
Ъгъл на улавяне. Важна характеристика на трошачката е ъгълът между челюстите, наречен ъгъл на скосяване (фиг. 4). Ако този ъгъл е много голям, тогава парчета материал могат да изскочат от гърлото; ако е твърде малък, тогава степента на смачкване ще бъде незначителна, тъй като бузите ще бъдат твърде близо една до друга.
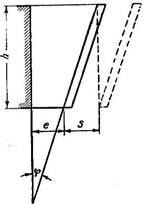
Фигура: 4. Да се определи броят на оборотите на челюстна трошачка.
За да не се изтласка материалът от устието на трошачката, е необходимо ъгълът на скобата да е по-малък или, в границите, да не надвишава два пъти ъгъла на триене (2р). Ъгълът на триене е средно 17 ° p = 0,3) и следователно максимално допустимият ъгъл на улавяне е cp = 34 °. Обикновено ъгълът на улавяне се приема в диапазона 15-25 °.
Скорост. При манивелните дробилки броят на оборотите е равен на броя на двойните люлки, докато при трошачките с гърбичен механизъм броят на двойните люлки е два пъти по-голям от броя на оборотите.
Нека обозначим според схемата (фиг. 4):
ъгъл на улавяне;
h-височина на слоя материал в работното пространство в cm;
e-стойност на сплайна при най-малкото отваряне в cm;
ход на s-бузата в cm;
e + s - стойността на шплинта при най-големия отвор в см и вземете K-броя двойни люлки на бузата в минута.
Нека приемем, че бузата се движи транслационно, тоест ъгълът const. Когато бузата се отдалечи от работното пространство със стойността s, слой от материал с височина
За да може този слой материал да падне от трошачката, продължителността на излизането на бузата от едно крайно положение в друго трябва да бъде поне времето t на свободно падане на материала под натиска на гравитацията от височина h:
С броя на двойните махове в минута К, продължителността на един удар на бузата:
Сравнявайки уравнения (а) и (б), намираме
Замествайки горната стойност за h, както и g = 981 cm/sec, определяме граничната стойност на K
Броят на двойните люлки, определен от това равенство, е максимално допустимият, тъй като при по-голям брой люлки материалът няма да има време да се изплъзне напълно през отвора в вратовръзката. Броят на оборотите на вала в челюстните дробилки обикновено варира в диапазона от 150 до 280 (при машини с голям капацитет) и от 300 до 450 (при машини с малък капацитет). На практика се взема броят на люлеенията в минута:
производителност. Както се вижда от диаграмата (фиг. 4), в едно двойно люлеене материал с обем V, равен на обема на призмата, височина b (дължина на работното пространство на трошачката в cm) и площ на сечението
Най-голямата ширина на изхода на трошачката може да се приеме равна на диаметъра d cm на парче материал след смачкване:
Със специфичното тегло на материала производителността на трошачката може да се определи по формулата
където е коефициентът на разхлабване на материала, равен на 0,4-0,7. Приблизително можем да вземем e = d и след това
Ефективността на челюстната трошачка на практика може да се приеме равна на средно -15 kgf/час на 1 cm2 от областта на гърлото, т.е.
където a е най-голямата ширина на гърлото в cm; дължина на гърлото в см.
Изискване за захранване. Аналитичното изчисление на необходимата мощност за челюстни трошачки дава неточни резултати. Следователно мощността на двигателя за челюстна трошачка се определя приблизително от емпиричната формула
където a е дължината на работното пространство на трошачката в cm; b е нейната ширина в cm.
А.Г. Касаткин
Основни процеси и апарати на химическата технология
(Глава XVIII. Смилане, пресяване и дозиране на твърди вещества/Грубо (предварително) раздробяване)
- Договор за услуга - за непрекъсната работа на гигантската челюстна дробилка на Metso в Русия - Списание
- RT-Khimkompozit "е разработил уникален офталмологичен материал за сложни хирургични операции
- Перлитна мазилка подробен преглед на строителния материал
- Тухлена плочка за вътрешна декорация, материални характеристики
- Пластмасата е вреден токсичен полимер или незаменим материал в съвременния свят