Мониторингът в реално време на работата на оборудването минимизира риска от инциденти
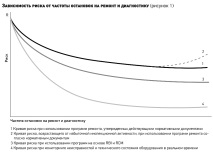
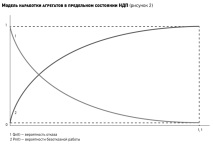
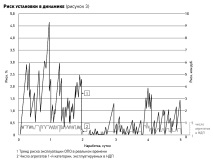
Работата на оборудването винаги е свързана с професионален риск. Постигането на абсолютна безопасност не е икономически осъществимо, тъй като води до неефективностпарични разходи. Следователно е необходимо да се управлява ефективно безопасността, като се използват системи от методи за анализ и оценка на съответните опасности с количествени показатели на риска. Разработването и усъвършенстването на такива автоматизирани системи се извършва от специалистилистове на изследователския и производствен център "Динамика". Днес те говорят за работата на компютърната система за наблюдение на риска от неизправности на оборудването в реално време за предотвратяване на аварии и технически контролкой е състоянието на оборудването 1 .
През последните години системите от стандарти, съдържащи понятието "риск", бяха сериозно развити в чуждестранни и местни нормативни документи. Много индустриални предприятия започнаха да създават системи за управление на риска в областта на индустриалната безопасност, за да оптимизират процесите на намаляване на разходите за техническиизвестна поддръжка и ремонт на оборудването (MRO). Нека отбележим редица характеристики на управлението на риска в областта на техногенната безопасност.
Първо, анулирането на риска е невъзможно, тъй като това означава прекратяване на работата на предприятието.работещи опасни производствени съоръжения (HIF).
На второ място, приемането на този риск също е невъзможно, тъй като заедно с нарастващата сложност и увеличаването на мащаба на промишленото производство на оризКи се увеличават.
Трето, прехвърлянето на този риск (неговата застраховка) е неефективно, тъй като най-тежките последици от инциденти винаги водят до непоправими загуби и не могат да бъдат компенсирани с никакви пари. Следователно трябва да се концентриратесъсредоточете се върху намаляването на риска.
Автоматичната диагностика на неизправности на оборудването ви позволява да наблюдавате процеса на неговото влошаване и почти да елиминирате риска от инциденти
Всички основни фактори, obusулавянето на високи експлоатационни разходи и загуби от аварии се проявяват чрез ресурса на оборудването, а общите щети директно зависят от навременността на откриване на неизправности и адекватността на действията на персонала при различни темпове на загуба на ресурси поради износване на елементите на оборудването. Колкото по-късно персоналът реагира на влошаването на състоянието на оборудването, толкова повече разходи ще бъдат необходими за възстановяването му и в случай на критична ситуация те дори могат да надхвърлят разходите за изграждане на нов технологичен комплекс.
От своя страна скоростта на реакция на персонала се дължи на две основни причини: наблюдаемостта на техническото състояние на оборудването и адекватността на реакцията при влошаването му, свързана с изискванията на ръководството и разбирането му за критичност. ситуации.
За тази цел е необходимо да се осигури мониторинг на оризаka пропускане на повреда на оборудването в реално време. С други думи, предоставете финансова оценка на текущото ниво на много вероятни разходи и загуби, които могат да бъдат направени от предприятието при съществуващите експлоатационни условия на оборудването (OPO), на мениджъри от всички редици.
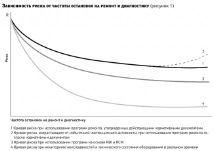
Технически данниоборудване, неговите неизправности, възникващи в него дефекти и най-опасните възли на блоковете се записват и представят от споменатите автоматизирани системитеми за всички нива на управление на производството. Системите са автоматичники, без участието на специалистдругари-диагностици, определят всички основни класове неизправности на динамичното оборудване и за всеки от тях издават редица предписания, автоматично диагностициратотстраняване на дефекти в центробежни и бутални компресори, помпи, въздушни охладители и редица други машини 2 .
Многократен анализ на ремонтните дейности, извършени съгласно предписанията на системите, показа, че всички изключвания на блоковете в състояние "Неприемливо" са наистина необходими. В 100% от случаите са потвърдени не само фактите за ремонти, но и дефекти на оборудването, които са били идентифицирани от автоматизирани системитеми.
- "Приемливо" (по-долу - D, единица зелен фон);
- „Изисква действие“ (по-нататък - TPM, жълт фон на устройството);
- "Недопустимо" (по-долу - NDP, червен фон на устройството).
За да се обоснове наличието на връзка между времето на работа на оборудването в различни състояния с последствията от негативни събития с тях, е необходимо да се определят такива събития и да се уточнят техните последствия, както и да се изчисли часъттова от тези събития, в зависимост от времето на работа.
Поради наличието на режим за спестяване на тенденция в автоматизирани системи, емпирични модели на функциите за разпределение на работата (времето на работа) на машините в техническитехните държави:
- D - от момента на стартиране до прехода към TPM;
- TPM - от момента на преминаване към TPM до момента на преминаване към NPD;
- NDP - от момента на преминаване към NDP до изключване;
- от момента на преминаване към TPM до изключване;
- от момента на прехода към NDP до спирането;
- от старт до стоп 3 .
Разпределението на Weibull - Gnedenko беше използвано за приблизително 4 функции на разпределение на времето за работа на възли и възли в различни технически състояния.
Имайте предвид, че в цикъла „спиране - приемливо - изисква действие - не е позволенотимо - стоп - ремонт ", помислетеПравят се само последователни промени в състоянията на оборудването. Получените коефициенти на теоретичните модели на законите за разпределение на времето за работа на машини, работещи в различни технически условия, имат доста високи стойности на мерките на Линдер (0,96 и по-високи). Тези данни потвърждават съгласието на получената теоретичнатехните модели за законите на разпределение на емпирични данни.
За да наблюдавате риска, е достатъчно да наблюдавате състоянието на оборудването
Времето за работа на блоковете в състояние D, т.е. от самото началоka единица до нейното преминаване в състояние на SST се характеризира с факта, че през този период ресурсът на единицата остава достатъчно голям 5 .
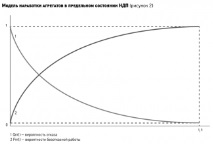
Когато блоковете се експлоатират в състоянията D и SST, рискът от пропускане на повреда също е налице, но стойността му е незначителна от гледна точка на влиянието му върху размера на риска. Грешките в изчисляването на риска се определят от редица фактори, включително грешката на системата за мониторинг, но нейното изчисляване може да бъде пренебрегнато, тъй като нашите изследвания използват данни от системи от 1-ви клас 6 .
Qopo (t) = 1 - Ropo (t),
Qopo (t) - вероятността за отказ на блоковете, експлоатирани в състояние на NDP;
Негативните последици от работата на блоковете в състояние на NDP са, първо, изключително висока вероятност за повреда и авария, която нараства с времето на работа в NDP състояние, и второ, голямата вероятност за спиране на производството, и трето, необходимостта от отстраняване на неизправността или дефекта на устройството, неговия ремонт.
Оценката на последиците от авария и загуби на централата помага да се управлява нивото на риска и да се разработи ефективна стратегия за управление на риска
Така че, според най-консервативните оценки, средната ценавъзстановяването след авария (SA) е около 15% от цената на оборудването на HIF, което за технологични инсталации в процес на изграждане в съвременни условия е около 100 милиона рубли, а периодът на възстановяване на ресурса на HIF е от седмица до два месеца.
Средната цена на престой на HIF (CS) в случай на повреда на оборудването е около 0,5 милиона рубли. на час, което се потвърждава от изчисленията, изготвени за някои рафинерии в Руската федерация. Според нашите оценки средните разходи за ремонт на изведен от експлоатация блок (СR) в състояние на MPC са около 0,2 милиона рубли.
От същите източници са известни и честотите на някои негативни последици, че позпозволява да се изчисляват вероятните загуби като сбор от горните видове загуби със съответните вероятности, а именно:
Copo = PA x CA + PS x CS + PR x CR,
РA, S, R - вероятност за идванеизбягване на последствията от инцидент, престой, съответно ремонт;
CA, S, R - съответно средни загуби от авария, престой и ремонт.
Ropo (t) = Ropo X Qopo (t),
През първите два дни персоналът на инсталацията чрез целенасочени и навременни действия значително намали броя на блоковете, експлоатирани в щата NDP, като по този начин постигна приемливо, от гледна точка на управлението на технологичния комплекс, ниво на риск от 0,2-0,5 милиона рубли.
Благодарение на наблюдението на оризаСлед функционирането на HIF в реално време, ръководството на рафинерията успя бързо да реагира на растежа на оризака. Това се потвърждава в раздела за тенденции от 3-5 дни експлоатация на комплекса. През този период увеличаването на броя на агрегатите в състоянието на NDP не е придружено от увеличаване на продължителността на тяхната работа в такова състояние, което се характеризира с размера на фиг.ка в такива моменти на ниво от 1,5-2 милиона рубли. Този факт от своя страна нагледно демонстрира оперативното изпълнение на инструкциите на ръководството от персонала, който вижда големината на риска от липсваща повреда на оборудването по време на работа на ЗЗО в реално време.
Автоматично изчисление и наблюдение в реално време фигКак да се пропусне отказът на HIF единици може да се извърши изключително от стационарни системи за наблюдение на техническото състояние на оборудването и да се представи на всички нива на управление на предприятието под формата на график (вж. Фиг. 3). Този подход на позиказва на ръководството:
- да не приемаме, а да познаваме съществуващото ниво на риск поради установената култура на производство в предприятието;
- да взема решения, насочени към намаляване на риска, тоест да осигури най-ефективната стратегия за управление на риска.
1 Костюков В.Н., Бойченко С.Н., Костюков А.В. Автоматизирани системи за контрол за безопасна експлоатация на ресурси за оборудване за рафиниране и нефтохимическа промишленост (ACS BER - KOMPAKS®). Изд. В.Н. Костюков. - М.: Машиностроение, 1999. - 163 с.
2 Костюков В.Н. Мониторинг на безопасността на производството. М.: Машиностроение, 2002. - 224 с.
4 Приблизително решение на сложна функция, използваща по-прости, което драстично ускорява и опростява решаването на проблеми.
- Бизнес идея за лазерен етикет, как да отворите, инвестиции, оборудване, какво ви е необходимо, за да отворите реални случаи
- Мониторинг на мрежово оборудване
- Компютърен томограф TOMO-KRS-MT - Медицинско оборудване, Медицинско оборудване, Медицинско оборудване,
- Компресор Kaeser Dental 3T - цена, снимка, реални спецификации, инструкции, ревюта
- Обучителен курс „Радиационна безопасност при експлоатация на радиационни източници