Приказката за това как се правят въглеродни влакна за една кола и как се опитват да я направят по-евтина?
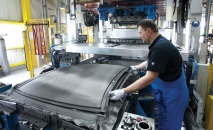
Автомобилните производители печелят високи печалби от използването на композитни материали. Един от тях е въглеродните влакна. Той ще бъде обсъден.
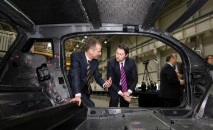
В автомобилния свят проникването на този материал от автомобилния спорт (където композитите от въглеродни влакна заеха гордо място преди 40 години) в новите McLaren, Corvette, Viper и по-достъпните спортни автомобили беше болезнено бавно. Въпреки че здравината и твърдостта на този лек материал са добре познати достойнства, при над 20 долара/кг (в комбинация с епоксидна смола) все още е твърде скъпо за използване в масово произвежданите автомобили.
За да смекчат това препятствие, автомобилните производители работят в тясно сътрудничество със съставни експертни компании, за да формират
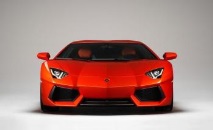
Стратегията на Моузес Лейк е вертикална интеграция, която беше използвана от Андрю Карнеги за производство на евтина стомана и Хенри Форд за изграждане на достъпен модел А с минимална печалба. Фабриката на Ford Michigan Rouge сглобява коли от стомана, желязо, стъкло, гуми и пластмаса, всички произведени в една сграда.
Елиминирането на посредника и самоуправлението на процесите на производство на въглеродни влакна също са ключови въпроси в автомобилния бизнес, тъй като съставният производствен процес е огромна част от цената на въглеродните влакна: средната му цена от 30 долара за кг е свързана най-вече с електричество, необходимо за превръщане на нишките. полиакрилонитрилна основа (C3H3N) във верига от въглеродни атоми, свързани в кристална структура.
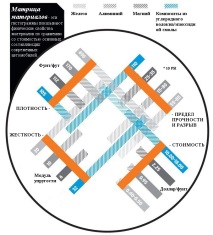
Вятърните турбини и слънчевите панели са модерен зелен източник на електричество, но са твърде зависими от времето, за да поддържат централата да работи постоянно. За разлика от гореспоменатите алтернативни енергийни източници, хидроенергията е зелен, надежден и достъпен енергиен източник. Именно поради тези три причини BMW и SGL построиха собствена фабрика за въглеродни влакна във Вашингтон. ВЕЦ на язовир Ванапум, разположен на река Колумбия, на 65 км от езерото Мозес, осигурява на фабриката BMW-SGL електричество с 2,8 цента на kW, което е 60 процента по-евтино от средната за страната цена на електроенергията за промишлени централи.
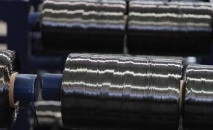
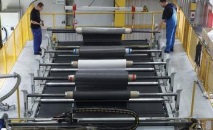
Друго съвместно предприятие, алианс между SGL и Mitsubishi Rayon Company, произвежда чисто бял полиакрилонитрилен материал в Отаке, Япония. Производственият процес е следният: след като материалът бъде доставен на езерото Мойсей, той се нагрява успешно при температура в диапазона от 200 - 300 градуса по Целзий. По време на нагряването цветът на материала постепенно се променя от бяло до жълто злато, след това мед и накрая кафяво, когато водородните и азотните атоми се изместват от полиакрилонитрила. След това влакната преминават през пещ за карбонизация, лишена от кислород, където температурата достига 1500 - 3100 градуса по Целзий. Тук цветът се променя на чисто черен и се образуват спретнато подравнени въглеродни кристали.
Последващият процес на окисляване разяжда повърхността на влакната, за да подобри връзката между въглеродните влакна и смолените материали, които ще задържат тъканите влакна на място, било то панорамен покривен панел или конструкция на тялото. В последния етап на производството автомобилните въглеродни влакна са покрити с епоксидна смола. След това петдесет хиляди нишки се навиват заедно на калерчета, за да се създаде прежда, наречена „канап“. Навита нататък произведените от калерчета въглеродни влакна за автомобили ще бъдат доставени в Германия. Там, в завода на BMW във Вакерсдорф, канапът от езерото Мозес се трансформира в плат от въглеродни влакна, който се доставя до Landshud, където се образуват отделни панели за електрическите автомобили i3 и i8. Рамкирането и сглобяването на каросерията на въглеродни влакна се извършва в Лайпциг, Германия.
Производство на въглеродни влакна BMW и SGL е една трета от цената на материалите, закупени от конкурентни доставчици. Други производители също са постигнали напредък в сложните процеси на композитно леене. Lamborghini и McLaren сега използват формоване на смола - вместо трудоемкия процес на ръчно наслояване и отнемащата време процедура на автоклавно втвърдяване - за да направят своя монокок. Готовата тъкан от въглеродни влакна, епоксидна пяна и алуминиеви вложки се зареждат в отворен комплект за мухъл от няколко части. След това комплектът на формата се затваря, точното количество епоксид се инжектира в него и необходимият панел се втвърдява в рамките на няколко минути.
В сътрудничество с Gallaway Golf, Lamborghini разработи друга алтернатива на автоклавното пресоване, наречена композитно коване. В този случай въглеродните влакна и епоксидът се компресират и инжектират в металната матрица, което води до лек материал с ниска порьозност.

- Резервни части за американски автомобили
- Как и какво да полирам автомобилно стъкло, стъклена полираща паста
- Онлайн магазин за автоаксесоари за чужди и местни автомобили
- Защитен филм за кола, кой да изберете
- Как да изберем детска обезопасителна система за вашата кола