Бои на основата на полиолефин - състав и свойства на боите
Състав и свойства на боите. Филмообразувателите в бои и лакове от полиолефинов тип обикновено са полиетилен с ниско налягане (HDPE) и полиетилен с високо налягане (LDPE), полипропилен, етилен-винил ацетатни съполимери (EVA), етилен-пропиленови съполимери (EPP) и акрилова киселина, смеси от полиетилен с каучуци, например полиизобутилен и др.
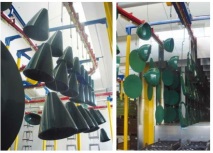
Най-подходящи за получаване на бои от HDPE са инжекционните степени с MFI в диапазона 2,5-6,0 g/10 min, с насипна плътност най-малко 0,25 g/cm3; LDPE се използва с MFR от 4-10 g/10 min. Заедно с индустриалните марки LDPE, частично може да се използва прах от вторичен полимер, получен например чрез механично или химическо смилане на използвания полиетиленов филм.
На основата на полиолефини се получават както пигментирани състави (бои), така и непигментирани състави (лакове). В допълнение към полимера, необходимите им съставки са стабилизатори, пигменти (за бои), вещества, които подобряват потока на стопилката; за подобряване на адхезията се въвеждат модифициращи добавки и покритията са необратими, структуриращи вещества.
Разработена е прахообразна боя върху LDPE клас P-PO-226 (TU6-10-102-75), немодифицирана и модифицирана с епоксиден олигомер от бял, сив и други цветове.
Типичните състави на основи на HDPE, приготвени на мястото на консумация, съдържат на 100 тегловни части полимер 0,5-1,2 части стабилизатори и 1-6 части пигменти.
Пигментите обикновено са газови сажди, титанов диоксид, хром оксид и алуминиев прах. В състава на съставите често се добавят модифициращи добавки - епоксидни олигомери, пентапласт, поливинил бутирал.
Условията за образуване на покрития от прахообразни полиетиленови състави се определят от марката на полимера, стойностите на MFI и дисперсията на праха. По време на електростатично пръскане, покрития от боя P-PO-226 се образуват при 220 ° C за 3-5 минути; когато се прилага в кипящ слой, продуктът се нагрява при температура 240-250 ° C и сливането на праха се извършва при 180-200 ° C за 3-5 минути за немодифицирана боя или 5-8 минути за модифициран. Композициите от HDPE изискват по-тежък режим на синтез: при 230-240 ° C, 2-5 минути.
В зависимост от предназначението се получават еднослойни покрития с обща дебелина 150-400 микрона. За предпочитане бързо охлаждане на покритията (втвърдяване) със студена вода.
За да се получат структурирани покрития, индустрията е усвоила производството на непигментирани състави 115-59 P (TU 6-05-05-64-76) на база LDPE, съдържащи дикумил пероксид. Структуриращият агент дикумил пероксид се въвежда в състава както чрез директно смесване, така и чрез третиране на праха или гранулирания полимер с неговия разтвор (т.нар. Дифузионен метод). В последния случай желаният ефект се постига вече с въвеждането на 1-2% (тегл.) Дикумил пероксид. Съставите, образуващи структурирани покрития, могат също да бъдат получени като се използват алкоксисилани като втвърдяващ агент. За да се осигури ефективното им взаимодействие, се използват прахове от вторичен или у-облъчен полиетилен. Покритията от термоструктуриращи съединения обикновено се получават при по-ниски температури (160-170 ° C) и по-дълго време за нагряване (12-15 минути).
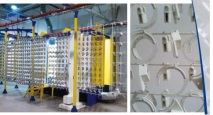
За приложение в електрическо поле с високо напрежение са разработени високодисперсни полиетиленови бои с висока скриваща сила. Те се получават чрез кристализиране на полиетилен от разтвор на повърхността на пигментните частици с последващо отстраняване на разтворителя. Средният размер на зърната на такива прахове е около 20 μm, а формата им е близка до сферичната. Боите позволяват да се получат тънки покрития с дебелина 20-40 микрона, характеризиращи се с повишена адхезивна якост.
Фирма Herbert Sintertechnik (Германия) произвежда прахообразни полиетиленови съединения-грунд Flamulit HP 11 и боя Flamulit RPE 25/06, предназначена за боядисване на тръби. Съставите са направени върху полиетилен с ниска плътност (хостален) с MFR 5.0 и 1.2, съответно. Грундът съдържа адхезивна добавка и има разпределение на частиците по размер: до 200 микрона-35%, 200-315 микрона-64,5%, над 315 микрона-0,5%. Боята (черен цвят) е по-грубо диспергирана, заедно с фината фракция, съдържа до 15% частици с размери 400-600 микрона. Препоръчителният метод за нанасяне на съединенията в кипящ слой върху повърхност на тръбата, предварително загрята до 300-320 ° C.
Полипропиленът, за разлика от полиетилена, има по-висока точка на топене (170 ° C); той е по-устойчив на напукване. За получаване на прахообразни бои се използва полипропилен с MFI до 8 g/10 min и размер на частиците не повече от 250 микрона.
Полипропиленът, когато се нагрява над точката на леене, образува относително ниско вискозитетни стопилки. Следователно, за да се приложи върху повърхността, е необходима по-ниска температура на нагряване на частите, отколкото в случая на полиетилен, а именно около 210-235 ° C. Изравняването на полипропиленовите покрития се извършва при 170-200 ° C, времето за нагряване е 2-5 минути.
HSE с ниско налягане по отношение на степента на кристалност и модула на еластичност се приближава до LDPE. Използват се и композиции, подобни на тях. Покритията от тях могат да се получат в широк температурен диапазон. При нанасяне на прах върху части, нагрети до 280-320 ° C, се образуват гладки прозрачни безцветни или светложълти филми, последвано от претопяване при 190-210 ° C за 5-8 минути. При високи температури (над 320 ° C) полимерът се разгражда силно. Това води до газово пълнене на филми, особено дебели.
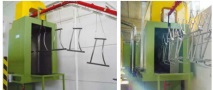
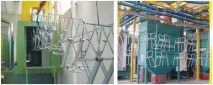
Bayer е усвоил производството на бои под търговското наименование levasint на основата на частично осапунен съполимер на етилен с винил ацетат, чиито покрития могат да работят при температури от -40 ° C и по-ниски.
Обещаващо е използването на смесени композиции от полиетилен-севилен. Въвеждането на севилен в полиетиленовите прахове улеснява условията за образуване на покрития, намалява тяхната твърдост и вътрешни напрежения и увеличава гъвкавостта и адхезията.
- Полимерни материали
- Кодиране на информация за знаци - MT1402 Теоретични основи на информатиката
- Основи на управлението
- Основи на безопасността на движението - Автошкола - Автопрофи
- ОТОПЛЕНИЕ НА ВОДАТА - Основи на водоснабдяването